Metalworking Equipment Maintenance Tips
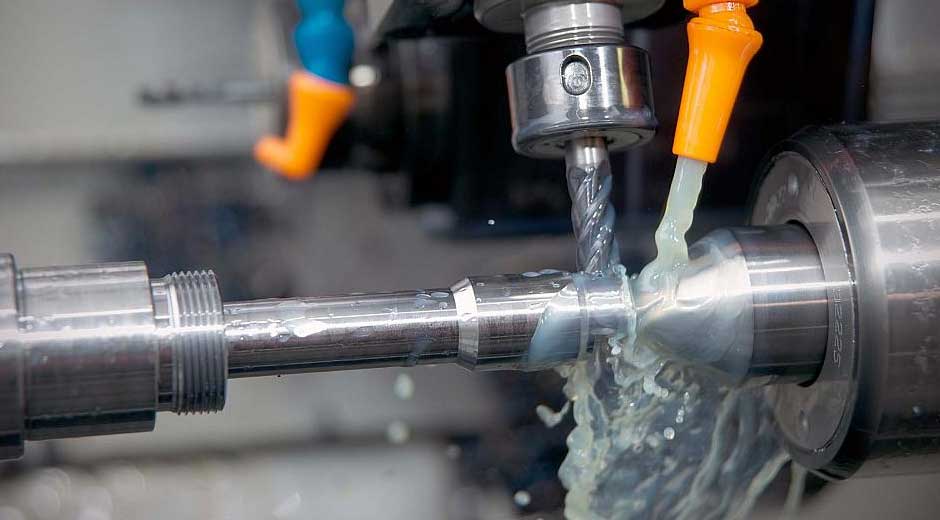
Metalworking equipment is a major component of the manufacturing and fabrication industries, which makes proper maintenance necessary to maintaine performance and durability. Proper maintenance improves accuracy, reduces downtime, and promotes safety in the workplace. Here are some metalworking equipment maintenance tips:
Use Proper Lubrication Practices
Wear and tear due to friction and heat build-up can result in reduced efficiency or mechanical breakdowns. The proper type and quantity of lubricant also help to reduce wear and tear and energy consumption. There are various types of lubricants for different machines, ranging from oils to greases and synthetics. Operators should consult the manufacturer’s guidelines to avoid incompatibility. If the amount of lubricant is too low, metal-to-metal contact may occur. If the amount is too high, dust and dirt may accumulate on the lubricant, forming dangerous layers.
Maintain Precision With Frequent Calibration
Machines need to be checked frequently to determine if they are still within the required production standards. Any misalignment of the tools, no matter how small, can cause errors in the final product and lead to a waste of material and time. Calibration entails confirming that the tools are in the right positions, the cutting depths are correct, and the moving parts are aligned. The use of precision tools such as dial indicators and micrometers is helpful in promoting accuracy. Regular calibration helps to maintain uniformity.
Keep Equipment Clean and Free of Debris
During operation, metal shavings, dust, and residue accumulate, which can impact the efficiency and safety of the machinery. Daily cleaning of the equipment helps to avoid the accumulation of dirt that may hinder the functioning of some parts, such as the cooling system. Using compressed air, industrial vacuums, and specific brushes confirms that all debris is cleared from the surface.
Operators should also make sure that coolant systems are clean and free from contamination or blockages. Filters should be cleaned or replaced periodically to confirm that the fluids are circulating properly. Lack of proper cleaning may result in overheating, corrosion, or reduced efficiency in cutting and shaping metal parts.
Check and Replace Worn Components
It is normal for metalworking equipment to undergo some level of wear and tear, but monitoring prevents unexpected failure. Periodic checks on gears, bearings, and belts help identify any signs of wear and tear before they worsen. A systematic approach to replacing worn-out parts reduces the likelihood of production downtimes and confirms that the machines are always in good working condition.
Operators should be very keen on any strange noises, vibrations, or declines in performance. These signs suggest that some components need to be addressed. Having a list of spare parts that are likely to be used in the course of maintenance helps reduce the time taken to maintain and source the spare parts when they are needed.
Utilize Proper Operator Training
Training helps the personnel to know the right way of handling, maintaining, and solving problems with equipment. Training should include the operation of the machines, maintenance procedures, and safety measures. Experienced operators are able to identify signs of wear and tear, improper calibration, or lubrication problems. When the employees are knowledgeable of the maintenance needs, they assist in the overall life expectancy of the machines. Regular training sessions confirm that the operators are aware of the latest trends in the industry and continue to adhere to the best practices.
Use High-Quality Tools and Components
The use of low-quality parts may cause wear and tear on the machinery, decrease efficiency, and, in some cases, damage the machinery. Buying high-quality tooling facilitates accurate cuts, consistent performance, and durability of the components. Using the right cutting tools for a particular job also helps to reduce the amount of pressure put on machines. Blunt or worn cutting tools can cause extra load on motors and heat generation.
Maintain Electrical Parts in Good Condition
Operators should inspect wiring, connections, and control panels for any signs of wear or heat build-up. Proper grounding of the machines improves safety and reduces electrical interference. Managing small electrical problems before they become big is helpful in maintaining the durability of metalworking machinery.
While preventive maintenance involves regular checks to prevent equipment failure, predictive maintenance uses data and technology to identify possible failures. Vibration analysis, thermal imaging, and sensors help identify problems with the machines. The wear and performance of the equipment can be monitored, and maintenance can be planned in advance without having to shut down operations. Through real-time monitoring, organizations are in a position to make the right decisions concerning the maintenance schedule, reducing the likelihood of breakdowns.
Find And Maintain Metalworking Equipment
Proper care of metalworking equipment promotes efficiency, accuracy, and safety. Listed above are some tips that you can follow to confirm that your equipment is well maintained and operations are not disrupted. If you want to purchase new machinery, select reliable suppliers. Buying from reputable sellers allows you to access high-quality, long-lasting, and efficiently supported equipment for your operations.