How ERP Facilitates Cross-Departmental Collaboration In Manufacturing
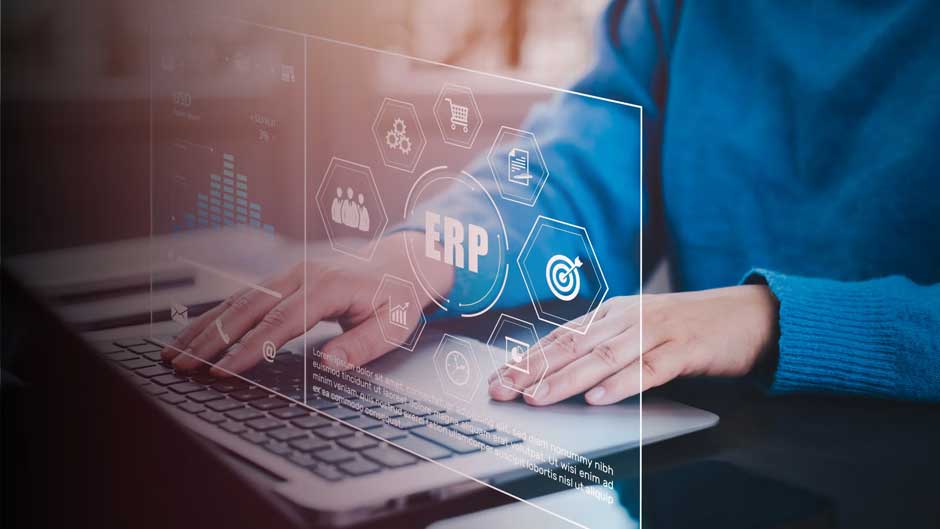
Within the manufacturing industry, efficient coordination among the various departments within an organization is obligatory in order to guarantee productivity, quality, and delivery schedules. However, several manufacturers deal with information that has been siloed, duplicate transactions, and miscommunications between various departments, such as production, procurement, inventory, finance, and sales. The gaps may lead to inefficient, incorrect and delays that impact on the whole supply chain. The right solution to these challenges is the implementation of manufacturing ERP software that combines the work processes and allows sharing information in real-time in the organization.
ERP manufacturing gives a centralized interface where all departments receive a single system and thus eliminates all fragmentation brought about by separate tools or spreadsheets. Having standardized data and an automated workflow, teams can become better coordinated, act in time, and share a common purpose. The integration is beneficial to the manufacturers because of its ability not only to coordinate internal activities but also react quicker to any demand or supply shocks or bottlenecks in production.
Improving Communication Between Departments
Improvement of communication between the different departments is one of the main issues where ERP helps in the enhancement of collaboration. In a conventional environment, various teams tend to have different systems thus contacting or authenticating vital information is quite challenging. Manufacturing ERP integrates data giving people a single source of truth, thus the same information is found with the engineers and planners, accountants, and warehouse workers. Such transparency reduces the instances of misunderstanding and the delays that result due to lack of complete or up to date communication between the relevant parties.
Built in works flows and automated notifications also lead to the ability of departments to communicate more efficiently. In other words, when a sales order is confirmed the production team is notified instantly so that manufacturing can be planned and the purchasing team can start ordering raw material. Finance can track costs and allocate budgets accordingly. Such smooth movements between phases enable teams not to arrange continuous meetings and handover data manually.
Supporting Real-Time Data Sharing
Real-time access to data is a crucial requirement to high functionality manufacturing overtime when several working groups require real-time information to complete their operations. The data provided by operations is continually recorded on manufacturing ERP systems, and it gives real-time access to every stakeholder of the entire production process, inventory, and supplier statuses among others. It removes the delay that can be present in the cases where departments use manually or unintegrated software.
Teaming up with the help and view of the live data will allow the teams to respond faster to any sudden events like a machine malfunctioning, a shipment lag, or a change in order. When production has gone off-schedule, the sales team can inform the customers ahead of time, and the inventory managers can focus on important stock. Organization becomes agile and able to give consistent performance when the flow of information of the real time is not blocked across departments.
Aligning Goals And Priorities
In a situation of silo departments, the department may work towards goals that are not aligned with those of the whole company. ERP in manufacturing assists in the coordination of departmental objectives with the provision of a common perspective into performance measures, resources, available, as well as high-level goals. All teams are able to track important indicators like the cost variation, rate of orders, and production efficiency with centralized dashboard clocks and reports. This alignment helps foster the idea of collective responsibility and it makes the departments work in a concerted effort to attain mutual results.
An example is that the purchasing department might desire to purchase materials at bulk to save on costs and the inventory managers are interested in reducing the stocks to reduce carrying costs. Through manufacturing ERP, such teams will be able to analyze the same data and reach the most acceptable trade-off according to the production schedules, storage room, and cash flow. This form of collaboration enhances general decision-making and avoids the case where each department works under its own interest to the detriment of the company.
Streamlining Approval And Workflow Processes
During the manufacturing process there are countless approvals required pertinent to the area of manufacturing, such as material requisition, budget authorization and change orders. These may involve several departments and can make the operations slow especially when not addressed responsibly. ERP manufacturing systems are also helpful since they provide approval of workflow and routing of tasks in an orderly and transparent manner. This cuts on delays, repetition of tasks and is geared towards adherence rules within the company.
Besides this, ERP work flows also assist in monitoring who authorized what and when and hence accountability and traceability arises. This comes in handy especially when auditing and looking at past performance. The ERP platform allows the departments to concentrate all their approvals, tracking, and approvals through the platform instead of using email trace files or using physical forms.
Enabling Collaborative Planning And Forecasting
The coordination that is so important during the planning process can be illustrated when conducting business planning in terms of budgeting, demand forecasting as well as production scheduling. They involve different departments, that is, sales, finance, and operations. This coordination in planning can be achieved with the help of manufacturing ERP software which can host the planning tools in a single place and engage different stakeholders who may coordinate the work over common plans that also share common data sets.
As an example, sales personnel are entitled to enter their demand forecasts in the system and the production planners use them to change capacity and material needs. Finance is then able to plan cash flow requirements and ensure the tracking of the budget. Synchronized planning of this sort results in overcoming more precise forecasts and less execution disruption. In case of coordinated work of the departments, it is easier to coordinate strategy with operations.
Conclusion
ERP in manufacturing is important in dissolving the organizational barriers among different departments and integrating a more integrated and responsive organization. It helps teams to collaborate with one another by enhancing effective communication, facilitating real-time access to information, and helping work collectively toward a common objective. Manufacturers can decrease manufacturing inefficiency, enhance decision-making process and build a leaner and more competitive business landscape using manufacturing ERP software. With manufacturing as it is, integrated systems will play an important role in establishing a formidable cross-departmental cooperation and a successful future.